Coal Mining 101: Out of the ground and onto the grid
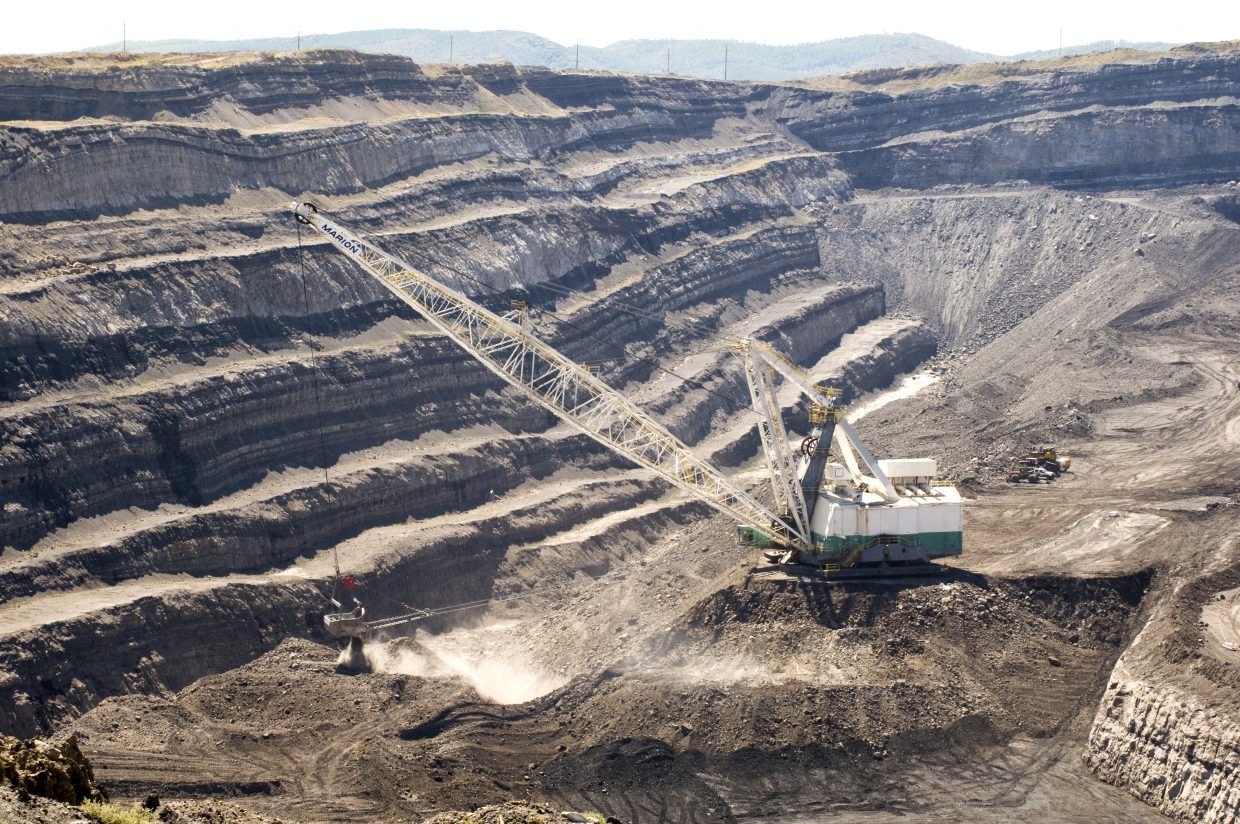
Lauren Blair
Though most of us benefit from the work done in a coal mine, few people ever gain a first-hand understanding of how coal gets from deep inside the ground and converted onto the electric grid.
Northwest Colorado sits on vast reserves of coal. The Yampa Coal Field covers 520 square miles in primarily Moffat and Routt counties, according to a U.S. Geologic Survey report. It extends 48 miles west to east from Lay to Oak Creek on the southeast side, and 33 miles north to south, as far north as Black Mountain.
Two kinds of coal mines exist in Northwest Colorado: surface mines, such as Colowyo and Trapper mines, and an underground mine — Twentymile.
There are four types of coal, the two most prevalent of which are mined in the Yampa Valley. Colowyo and Trapper mines both extract sub-bituminous coal, while Twentymile extracts bituminous coal. All three mines tout the low sulfur and ash content of their coal, criteria which make for cleaner burning fuel.
Bituminous coal has higher BTU — or British Thermal Unit, which measures the amount of energy it can produce — and is the most abundant coal in active U.S. mining regions, according to the U.S. Energy Information Administration. However, subbituminous coal can be found in thick beds near the surface making it cheaper to mine, and is also well-suited as fuel for electric power generation.
Both surface and underground mines utilize modern engineering and high-tech equipment to help them safely and efficiently remove coal from the earth using extremely different processes.
Surface mining 101
At a surface mine, coal is removed by digging through layers of earth in order to reach and remove seams of coal that lay beneath the ground.
The process of surface mining begins with exploratory drilling, which provides data to create a geologic model of the ground beneath. Holes are drilled into the ground at regular intervals to remove samples of earth from as deep as 1,000 feet below the surface.
Engineers then examine the model to determine where the coal seams are, how thick they are, and how thick the layers of earth, or “overburden” are in between them.
“From there we can figure out the economics and the right places to dig and what’s going to be the most effective and efficient way to mine that area,” said Colowyo Coal Company Mine Manager Chris McCourt.
The geographic model looks something like a giant layer cake, with thick layers of overburden separated by thinner layers of coal in a ratio of nearly 10 to 1 at Colowyo. There, the “cake” consists of 13 layers of coal which range anywhere from 18 inches to 18 feet thick.
“We have a lot of material we have to move to get the one unit of coal,” McCourt said. “It can be anywhere from a few feet to a few hundred feet to get to the next coal seam.”
The mining process begins with removing the topsoil layer — typically ranges from 6 to 24 inches, according to an informational pamphlet from Trapper Mining, Inc. — and carefully storing it at another site, to be replaced once mining is complete.
After the topsoil has been removed, the overburden layer — up to 200 feet thick at Trapper Mine — above the first coal seam is blasted to make it easier to dig and to break it up into manageable pieces. Overburden is either placed in an adjacent section of the pit where the coal has already been removed, or hauled away from the pit site and stored in large dunes until the reclamation process begins.
Once the coal seam has been uncovered, it is blasted and removed in the same fashion, and is then scooped into 4-story tall haul trucks, which carry it to a stockpile site.
The machine which does the heavy lifting in the mine pit is called a dragline, which can weigh as much as 3,100 tons. It looks like a crane and a bulldozer combined, with a cab as large as a house and a boom up to 325 feet long. The bucket attached to the end of the boom can move upwards of 80 tons of overburden at a time.
As the mine progresses, it expands both horizontally and vertically. At Colowyo, machines remove coal in vertical slices, and begin filling in overburden and reclaiming land behind them as they go.
Another process utilized to remove more coal once a mine has been dug to its deepest point involves a machine called a high wall miner. The high wall miner is capable of mining underground without requiring manpower underground; it can dig up to 1,000 horizontal feet into an exposed seam, pulling out the coal with flat cars sent in to retrieve it.
From the stockpile, coal from different sites and different seams is blended together to to meet certain quality standards and stored in a central stockpile.
“Once we dig it out of the ground, each of the 13 layers has a little bit different quality: sulfur and BTU. We blend it together so it’s a consistent product,” McCourt said.
The coal passes through two more crushers to create a uniform consistency on its way to being loaded out of the mine. At Trapper Mine, it is transported by truck straight to Craig Station, and at Colowyo, it is trucked to the rail head near the entrance of the mine, where it is loaded onto trains and shipped directly to Craig Station.
After land is mined, it needs to be put back together. The reclamation process involves three phases, and begins before ground is ever broken on a new pit.
“It actually starts before the coal is removed with studies to determine the natural state of the vegetation, wildlife, soils, water, air, surface contours and land uses,” according to Trapper Mine’s pamphlet.
During phase one, the overburden that was removed in the process of extracting the coal is replaced and contoured to match the original landscape.
In phase two, the topsoil which was set aside at the start of the mining process is replaced and reseeded with seed mixes which are regulated by the Colorado Division of Reclamation, Mining and Safety.
In phase three, the vegetation is fully reestablished, and phase three bond release indicates land that has been fully reclaimed, which requires, at minimum, a 10-year process.
Trapper Mine, which received a special honors from the U.S. Department of the Interior and Office of Surface Mining for its reclamation success, boasts abundant wildlife on its reclaimed lands from black bears and mountain lions to over 100 species of birds to flourishing wild game populations including antelope and elk. Colowyo is similarly home to large herds of elk which winter over in reclaimed lands surrounding the mine.
Underground mining 101
Visiting a surface mine may be like stepping foot onto another planet, but going underground is like stepping into another world altogether. An underground mine produces the same end result — coal — but uses a completely different process.
Rather than giant trucks and draglines spread out across vast expanses of dirt and deep pits connected by wide, winding roadways, an underground mine consists of uniform tunnels laid out in a carefully planned grid deep under the earth. Miners at Twentymile Mine in Routt County do their work about 1,300 feet below the earth’s surface.
The tunnels, called “entries,” are dug by a machine known as a continuous miner, which eats its way through the coal at a rate of up to 250 feet per 12-hour shift as it paves the way for the main event, the longwall operation. Twentymile operates two continuous mining machines, which create tunnels 9 to 10 feet high and 20 feet wide, producing up to 5,000 tons of coal per day.
The tunnels dug by the machines are like the streets on a city grid, while the city blocks are the panels of coal which are mined using the longwall method. Panels at Twentymile are 1,000 feet wide, nine feet tall and anywhere from 2,500 to 18,000 feet (or nearly 3 and 1/2 miles) long, according to Twentymile General Manager Pat Sollars.
As the continuous miner digs new entryway, a roof bolter follows behind to stabilize the roof by essentially laminating it with resin and bolts up to 8 feet long, which are drilled into the ceiling every five feet. Added protection is provided by mats and mesh applied to the ceiling to contain loose material from the shale roof.
Because coal dust is highly ignitable, every exposed surface underground is sprayed with rock dust made of pulverized limestone, which also serves to brighten the walls of the mine.
“You put limestone everywhere to ensure that the top 1/8 inch of all surfaces in the mine is 80 percent incombustible,” Sollars said.
Once the tunnels have reached their full length and have provided access to the coal panel, a dizzying array of equipment — consisting of six main components — is set up to begin the longwall operation.
First are the shields: massive, steel canopies which press into the roof to keep it from collapsing. One hundred and fifty shields are lined up side-by-side to create a kind of 1,000-foot-long, underground hallway adjacent to the face of the coal seam being mined. Held up by two electro-hydraulic legs, each shield can hold up to 1,300 tons of weight, and are automated to essentially walk themselves forward as the coal is mined and the face of the longwall retreats.
As the shields move forward, the roof behind them collapses.
Second is the shearer, a machine equipped with two steel-toothed, cylindrical drums that eat into the face of the coal seam. Protected under the canopy formed by the shields, the shearer rides back and forth along the 1,000-foot-wide panel, cutting up to one meter deep into the coal face with each pass, according to Sollars.
“Moving at a rate of up to 130 feet per minute, the shearer removes or cuts about 1,300 tons of coal for each one meter of advance in the process,” Sollars said.
The shearer — and the entire longwall operation — advances 60 to 80 feet into the panel each day. A longwall miner can walk up to 10 miles per shift as he makes as many as 25 roundtrips per day back and forth along the 1,000-foot panel, according to a video produced by Peabody Energy titled “Twentymile Coal: The People Behind The Power.”
The coal that is removed from the face by the shearer is caught by a highly engineered and rugged conveyor system, known as an armored face conveyor, the third component. The AFC carries the coal away from the face and brings it to the fourth component, the stage loader, which is another chain conveyor with a crusher built into it.
The stage loader crushes the coal to a more manageable size to be transported to the surface on yet another conveyor. Twentymile has six miles of five-foot-wide conveyor belt, powered by 28,000 horsepower, which can carry 5,000 tons of coal an hour to the surface, according to Sollars.
Two more components enable the underground operation: the emulsion pumps, which provide fluid to the hydraulic shields to allow them to do their job, and the power train, which delivers 4,160 volts of power to the longwall via a “monorail” system. Dust and oxygen levels are also scrupulously monitored to ensure air quality inside the mine.
“Directing the flow of air underground is an important part of the mining operation. Large surface fans pull 1 million cubic feet of air through the mine each minute, drawing dust and gas away from working faces and supplying miners with fresh air,” according to the video.
Once the coal reaches the surface, it is washed to remove rock sediment, crushed and loaded daily onto one to two unit trains of over 100 cars, carrying up to 25,000 tons of coal per day to customers primarily in Colorado and the western United States, including Hayden Station.
The underground mine relies on diligent maintenance of each of the components and steps in the process to ensure the safety and efficiency of production.
“It’s like a little city, because you have to have an infrastructure in place before any mining can happen,” Sollars said.
Once a panel has been completely mined, which can take anywhere from two to 10 months, the entire infrastructure must be disassembled and moved to a new panel. Twentymile is currently in the process of moving the longwall to a new 8,000 foot panel.
All told, crews at Twentymile must transport 7,546 tons of equipment every time the longwall is moved, with the heaviest components weighing in at 40 to 60 tons a piece. A longwall move typically takes 18 to 22 days, and happens on average two to three times per year.
With crews dedicated to providing for every element of the complex underground operation, and a vast vocabulary that is unique to underground mining (and practically unintelligible to a non-miner), the underground mine truly is a world of its own.
Contact Lauren Blair at 970-875-1794 or lblair@CraigDailyPress.com.

Support Local Journalism

Support Local Journalism
Readers around Craig and Moffat County make the Craig Press’ work possible. Your financial contribution supports our efforts to deliver quality, locally relevant journalism.
Now more than ever, your support is critical to help us keep our community informed about the evolving coronavirus pandemic and the impact it is having locally. Every contribution, however large or small, will make a difference.
Each donation will be used exclusively for the development and creation of increased news coverage.