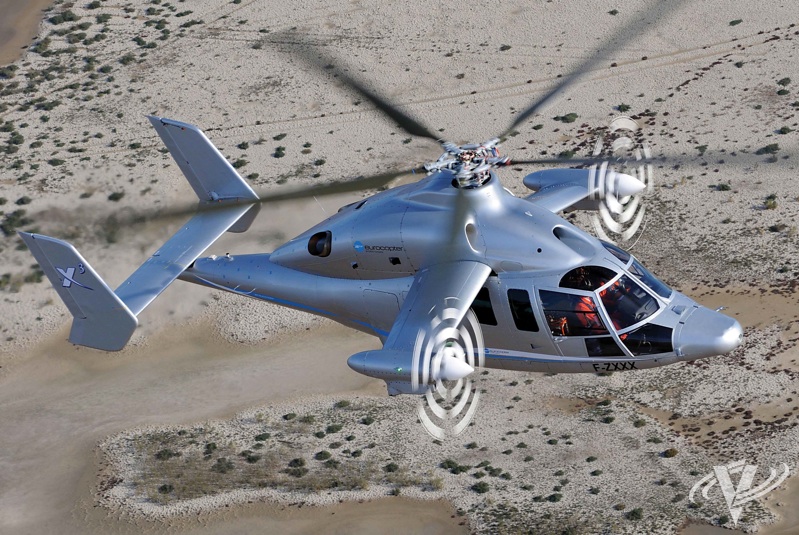
Eurocopter’s X-cubed is one of the helicopter industry’s new high-speed prototypes. Patrick Penna/Eurocopter Photo
Pure helicopters have been hobbled by an upper speed limit since turbine engines gave us enough power to push to that limit of about 160 knots in level flight. Simply stated, using the main rotor to provide upward lift and forward thrust isn’t that efficient. While some research projects many years ago pushed back the edge of the envelope, there were too many compromises to take these machines to either civil or military operational use.
The dream of going faster hasn’t died, though, and recent advances in materials, knowledge and computing power have combined with the political will to produce something approaching a realistic possibility.
The main concepts currently in play are the tilt rotor (Bell-Boeing V-22 and Bell/Agusta BA609), the co-axial compound helicopter (Sikorsky X2), the single-rotor compound (Piasecki SpeedHawk) and the single-rotor plus propeller (Eurocopter X3 or X-cubed). The Russians have their own solutions, but these are all slight variants on the four just mentioned, and so far only drawings and models have emerged. One of the interesting things about these concepts is that they all have slightly different approaches to the same aim, and competition will improve them all: the marketplace is a pretty tough proving ground.
Bear in mind all these concepts retain all the necessary qualities of a helicopter – namely, the ability to maintain position with winds from any azimuth and to climb vertically.
All of the concepts are similar in that the main rotor is offloaded from the requirement to produce forward thrust. (Various forms of propellers are used to push the machines through the air, and to slow it down, as well.) When the rotor is not required to be tilted steeply forward, the blade pitch on the retreating blade can be reduced, with many benefits. The first benefit is the retreating blade now operates at much lower angles of attack and hence farther from the stall at the same airspeed as a normal helicopter. It means you can fly at a higher airspeed before you start to see the effects of stall. This has a huge effect on the loads placed on the blades, which is a much larger problem than most of us realize.
The Piasecki concept goes one step farther in regards to offloading the main rotor by having a large lifting wing, which it recently increased in size so it now stretches to nearly the full diameter of the main rotor. The Eurocopter X-cubed has a small wing, but it appears to be more to hold the propellers than to provide lift. The Sikorsky’s co-axial rotor concept, meanwhile, inherently reduces the lift that any one rotor disk has to produce.
Since there are competing designs in place, let’s look at some of the tradeoffs and technical challenges each may face. We’ll leave out the V-22/BA609; the tilt-rotor concept has been around for quite a while and is reasonably well understood.
Sikorsky X2
Being a co-axial rotor obviously means having another set of whirling, rotating wings with all the attendant complexities of control, vibration, stresses and strains. And, it’s still a rotor system, subject to all the issues that come with this.
While having a pusher propeller in the mix means the main rotors no longer have to produce forward thrust, they still need to produce all the lift, which means they must operate at the same pitch angles as other main-rotor-only systems. These pitch angles change a lot more than if the rotor were offloaded to a greater degree, and this requires more structure and induces more vibration that has to be eliminated one way or the other.
I attended Sikorsky’s public demonstration of the X2 in October 2010 (see p.17, Vertical, Dec’10-Jan’11 or see Vertical Online) and found the company had put a lot of effort into vibration control on the X2, as this was a serious problem on the much earlier XH-59A. The yaw control I saw, via differential collective pitch on the two rotor heads, was not a new concept, although all the other co-axial designs have featured much larger vertical stabilizers than the X2, which is just a proof-of-concept designed mostly for speed. Lastly, the rear prop can be used to slow the machine as well as push it, so there will be less pitch attitude movement of the airframe to change airspeed, and the cruise pitch attitude can be optimized for minimum drag.
Sikorsky also used the October demonstration to announce its follow-on development program for the X2: the S-97 Raider. This proposed model represents a sizeable investment to mature the design and establish a brand-new light helicopter. Sikorsky is targeting the S-97 toward the United States military as a potential light armed reconnaissance helicopter, and will build two more prototypes over the next four years for military evaluation.
Piasecki X-49A SpeedHawk
One of the advantages of using a wing to offload the rotor from the need to produce lift is that lower blade pitch angles can be used in all cruise conditions, which is the where the cyclical change in pitch and aerodynamic loads really create havoc.
I had the pleasure of talking with John Piasecki, president and chief executive officer of Piasecki Aircraft Corp. and the driving force behind the X-49A, to learn a bit more about the SpeedHawk, which applies the offloading concept to a modified Sikorsky H-60 Black Hawk. The first flight of the SpeedHawk occurred on June 29, 2007, and the aircraft has now completed its Phase 1 flight test envelope expansion.
The company’s testing has already shown remarkable reduction in stresses and strains on the rotor hub and components compared to the baseline H-60. But, the disadvantage of the wing is that it sits under the main rotor and is subject to downwash in the hover, which hurts hover performance – which is the main reason for helicopters! (The proposed solution is to have the leading edge of the wing tilt/rotate to a near-vertical position in the low-speed regime.)
The additional weight and complexity of the wing and ducted fan are about the same as the savings in weight that could be made in the rotor head compared to the co-axial concepts. Given that Piasecki is forced to use an existing airframe that is certainly not optimized for speed, it’s unlikely the full advantages of the savings possible from a truly optimized wing/fuselage/rotor head will be seen in the near future. (John Piasecki, though, did confirm the large number of small improvements that could be made if the company was starting from a clean sheet of paper.)
The movable, ducted fan/thrust bucket (what the company calls the vectored thrust ducted propeller or VTDP) at the back end is necessarily heavier than just a propeller, but does provide a large moment-arm for yaw control and anti-torque. The interesting engineering challenge to integrate the VTDP into the control system appears to be well in hand.
Piasecki has also just installed a third engine (Rolls-Royce 250-C30) to provide additional power to the VTDP to permit all the normal engine power to go to the main rotor for hover performance – a challenge that was met with the typical ingenuity one has come to expect from good engineers!
Eurocopter X3
The Eurocopter X-cubed “props-on-wings” concept adds some new twists and challenges to the discussion. The X-cubed’s first flight was on Sept. 6, 2010, and it was formally unveiled in late September at the French military’s secure Istres proving ground (see p.16, Vertical, Dec’10-Jan’11 or see Vertical Online). The X-cubed airframe comes from the Dauphin AS 365, the main rotor from the EC 155 and the main module of the main gearbox from the EC 175. It has two conventional five-bladed propellers in line with the five-bladed main rotor, all powered by twin Rolls-Royce Turbomeca RTM322-01/9 turboshaft engines.
Yaw control will be through differential propeller pitch, which will be interesting in side winds when one propeller is blanked by the fuselage. It will also mean that air is being blown forward and backward around the fuselage, which when close to the ground will make for some interesting flow patterns. The wing is relatively low, meaning any power changes in flight will affect the pitch attitude (an increase in power will tend to pitch the nose opposite to a reduction in power to a much greater extent than we’re used to). How these propellers would be used to slow the machine down without having a major effect on the airflow over the small wing is not known. (A rear-mounted prop such as Sikorsky and Piasecki have employed can be used in reverse with little effect on the rest of fuselage.)
The disadvantage of having two propellers means there is something else to fail. It’s also assumed that the props would be shut down once on the ground – otherwise loading and unloading the aircraft becomes a real issue!
In the last set of tests for its Step 1 phase, Eurocopter reported that the X-cubed reached its speed objective of 180 knots of true airspeed in level flight “at a reduced level of engine power.” In the Step 2 phase of testing, the next milestone the company hopes to achieve will be a cruise speed in excess of 220 knots.
In addition to speed, stability and handling characteristics have also been explored in the completed set of flight tests. “The flight envelope has been opened with and without autopilot to validate the basic hybrid demonstrator aircraft’s stability and handling characteristics,” stated the company in a Dec. 9 press release. “The X-cubed has reached an altitude of 12,500 feet and performed maneuvers with left and right turns at bank angles of up to 60 degrees.”
Some Additional Points
Redundancy of control: An interesting side effect of the Piasecki concept is that there is the possibility of redundancy of control – more than one control surface can be used to manage the helicopter. And, with the large number of possible controls, they can be mixed and blended to optimize performance for a mission: for example, the wing might be partly tilted for maximum lift at “low-ish” speeds, to optimize the lift/drag ratio thereby reducing fuel flow and improving loiter time, if that’s a mission requirement.
Overcoming drag: Streamlining is an issue with anything attaining speeds of more than about 50 knots. Drag increases as the square of the speed, and anything that isn’t sleek and streamlined is going to pay the price. Sikorsky is the hands-down winner on this front as it started from a clean sheet of paper and achieved probably the best drag reduction of any helicopter. Even the rotor mast is being given a fairing in the next stage.
Piasecki is working with a large handicap in utilizing a very draggy H-60 airframe. The SpeedHawk’s next iteration will see a lot of drag reduction, but the large and complex rear fan arrangement will always add more drag than the Sikorsky concept.
The Eurocopter machine started with an already streamlined fuselage, so it’s somewhere in between the other two main contenders.
The Benefits of High Speed
What are the benefits of high-speed helicopter flight? The cruise airspeeds of the high-speed concepts now all comfortably reach into the low 200-knot region or thereabouts. For those already cruising at 150 knots – and there are not many civil helicopters that can do even this – that’s a 30+ percent improvement in speed. For those lumbering around 100 to 120 knots, this is nearly double.
Increased airspeed has an interesting effect on airborne time. Everywhere I go, it seems there is a headwind, and in a slow helicopter (100-knot cruise speed), even a light wind has an appreciable effect on a 100-mile flight. A 20-knot headwind in this case makes the flight about 13 minutes or about 25 percent longer. But, when the cruise airspeed is 200 knots, a 20-knot headwind lengthens a 100-mile flight by only about three minutes or 11 percent. You can do the math yourself on other distances and wind speeds to see the difference it would make on your flights.
Since most of the time machines with this speed are going to be flown instrument flight rules (IFR), it only makes sense that they have the speed to match most of the fixed-wing aircraft they’ll be mixing with.
However, for short trips (less than 50 miles or so) there isn’t much benefit to a high-speed helicopter, unless time is really critical. Those who say helicopter emergency medical services is an obvious market don’t realize that most of the time the helicopter already gets there well ahead of when the patient is ready to transfer.
Not for Everyone
Helicopters are useful for their unique capabilities of landing and taking off from very small areas. They’re not typically used for long distance travel, as they are just too slow compared to any fixed-wing aircraft. This combines to make them “local” aircraft: they don’t normally stray too far from home.
The speed improvement being sought will change all that. While helicopters won’t become transcontinental machines, these compound ships will become regional aircraft. A radius of action of 200 miles will now (if you can justify and afford it) be possible.
Of course, you’ll need to be able to afford it – and initially the new users will be militaries, who also will open up new roles for the helicopters. Just as tactics are changing because the V-22 can lift troops quickly over long distances, a faster helicopter will have new roles and will only increase the military’s use of rotary-wing aircraft (assuming the UAVs don’t take it all away).
Change and Constancy
There have been lots of new concepts that have had teething problems. For example, the Learjet was well understood to be both a jet and a high-altitude machine when it came out, but there were still lots of growing pains not related to the design/technical aspects.
High-speed helicopters are not going to be any different in this respect, and for insight into this I spoke with the U.S. Federal Aviation Administration’s Hooper Harris, one of the few people (let alone government officials) I know with feet in both fixed- and rotary-wing camps. His comments were intriguing and insightful: “Pilots will have to worry about more than local weather, now it’s regional weather that becomes an issue. To make maximum use of the range/speed improvements, it will probably be necessary to fly IFR nearly everywhere, and the problem here is that helicopters don’t always operate to and from airports, which is where the IFR infrastructure is set up. There are going to be challenges that go beyond the technical issues, and I hope both the FAA and the users can rise up to meet them safely.”
Still, single-rotor helicopters aren’t going to be replaced en-masse by these compound machines. There are some things the single rotor does much more cost-effectively than anything else. But, the changes are coming, and we need to be prepared for not just the technical challenges, but the myriad of other changes that will accompany any new concept.